Management is the basis for quality management
Quality management is fundamentally the same as quality of management. Then, if somebody tries to understand it, he or she should at first clearly recognize what is management all about. There is a huge amount of literature and other kinds of references dealing with management concept, theories, principles, and practices. That has made the whole topic very complicated. However, one of the most well-known and evergreen management model, so called Deming or Shewhart cycle, or PDCA model (see the figure), is very simple but nevertheless very useful also in the context of quality of management.
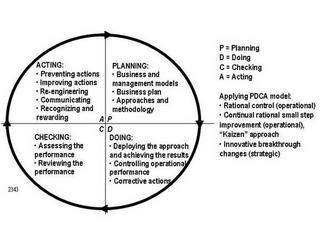
PDCA model describes how a consistent management consists of four consecutive activities:
- P: Planning the business activities what should be done and what results should be achieved
- D: Getting done the business obligations according to the plans
- C: Checking what was done and what results achieved
- A: Acting rationally taking into account the observations and results of the checking
PDCA model can be applied both in application of strategic and operational management of any organization. At the strategic management level one makes decisions and undertakes measures concerning the entire organization and considers especially the future competitiveness of the organization, and the operational level of management means decisions and measures to manage daily activities on operational sites.
In organizational environments the PDCA model may and should be applied in three different scopes:
- Control: Managing daily operations in business processes in order to achieve the specified results of the doing. Normally rectifying nonconformities is carried out in connection with control. Control is based on operational plan and objectives. Control is fundamentally a rational activity on the basis of explicit facts.
- Prevention and operational improvements: This means especially solving acute problems, preventing nonconformities, and finding / implementing operational step by step improvements in business processes. For continual improvement one can also use a well-known concept "Kaizen". Prevention and continual improvement are also very rational and facts based activities.
- Breakthrough improvements: This includes innovating and implementing strategically significant changes in the way doing business. Breakthrough changes cannot be based only on facts and therefore it emphasizes needs from visions and measures of innovation that are mainly tacit (implicit) knowledge issues.
Top business leaders (senior executives) are responsible of the breakthrough improvements. Control, prevention, and small step improvement should be carried our by the responsibility of operational managers.
2 Comments:
The PDCA model was originally introduced by Walter Shewhart already in 1929 and published in his book 1939. In that original version Shewhart used S (Study) instead of C (Check). Shewhart used this approach particularly for statistical quality control of manufacturing processes.
World-widely the PDCA model however became well-known through W. Edwards Deming. It was an essential managing instrument in his lectures in Japan from 1950 to 1965 to Japanese business leaders, and later also in his popular lectures in the USA from 1980 to 1993. Deming called the model as Shewhart cycle according to its inventor and its graphical form. People very often call the model also as Deming’s Wheel. Deming published the methodology e.g. in his book Out of crisis (1982). For Deming the PDCA model was “a flow diagram for learning, and for improvement of a product and a process”.
PDCA model corresponds to the general principle of managing a system according to the general systems thinking, systems dynamics, or cybernetics. Also Joseph Juran’s Trilogy model includes the same action elements as the PDCA model. Masaaki Imai’s Kaizen methodology for continual improvement is also based on the same origin. Shoji Shiba (1997) has combined the model with Ikujiro Nonaka’s knowledge-conversion process and expression SECI (Socialize, Externalize, Combine, and Internalize). In this context Shiba emphasizes the importance of intuition and innovation for breakthrough improvements. Shiba (2005) has also shown the connections of the model to the Buddhist thinking. However, he still considers also control, problem solving, and continual improvement as relevant and important applications of the PDCA model.
A modern application of PDCA model is SixSigma methodology for an organization’s performance improvement. Its activity phases are DMAIC – Define, Measure, Analyze, Improve, and Control.
Wasn't it so that C was originally S and stood for study?
Post a Comment
<< Home